NFRC Technical Manager Gary Walpole visited JPR Roofing and Flooring Limited to understand how they tackled this complex Safe2Torch project.
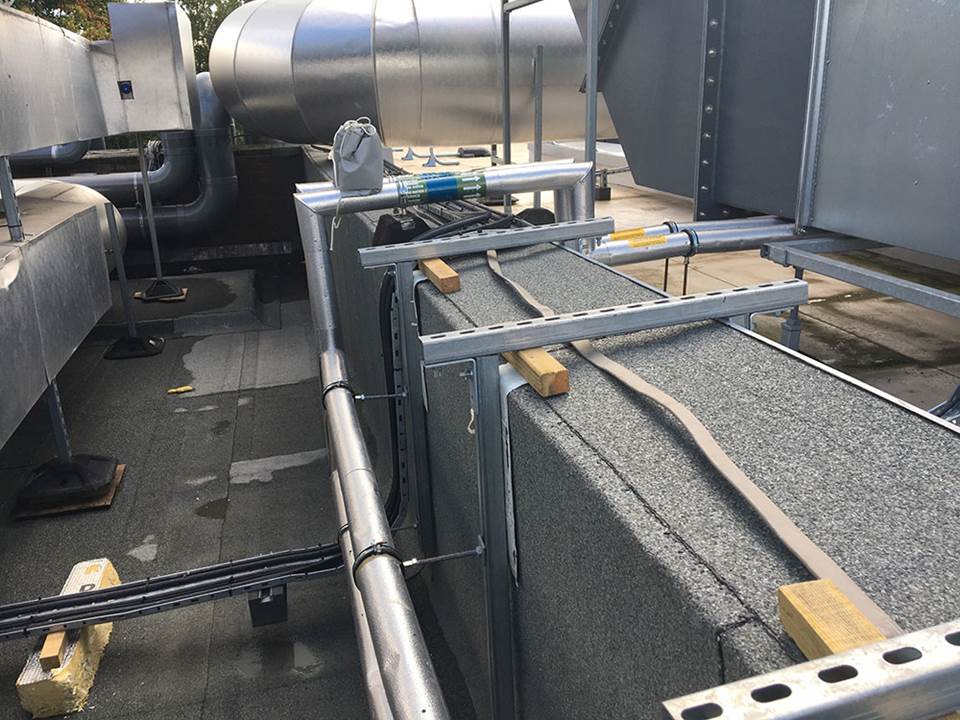
Keele University is a public research university located about three miles from Newcastle-under-Lyme, Staffordshire where JPR Roofing and Flooring Limited (JPR) were tasked with overlaying a complex roof over a laboratory where 18 months earlier services and plant had been installed for the labs.
This meant that gas torches, even for drying, would not be permitted, making an already complex project more challenging. Another issue that had to be factored in was the need for a waterproof covering robust enough to cope with M&E engineers accessing the services for ongoing maintenance.
Pat Llewellyn, managing director at JPR, therefore needed to work closely with the manufacturer to determine the best waterproof covering to suit this project. Even though there were areas clear of services where it was possible to use a gas torch, it was agreed that a full Safe2Torch system should be specified, to ensure the whole roof system was flame-free.
Being such a complex Safe2Torch project, I was invited to see the installation process for myself and to discuss with the team how they had found the transition from traditional torch-on RBM systems to self-adhesive and hot-aired welded systems.
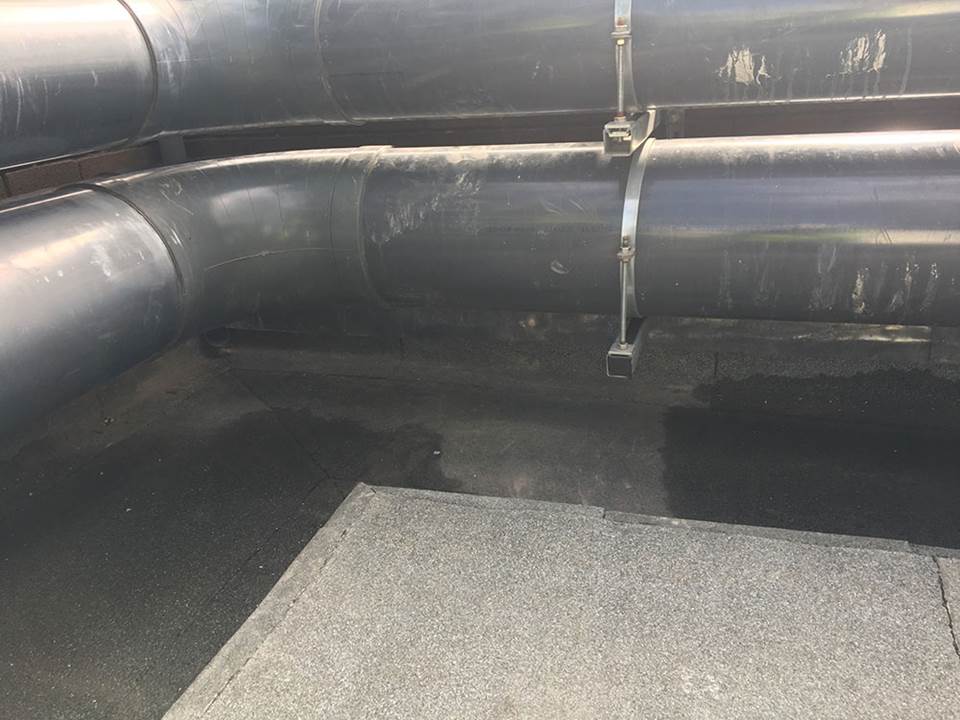
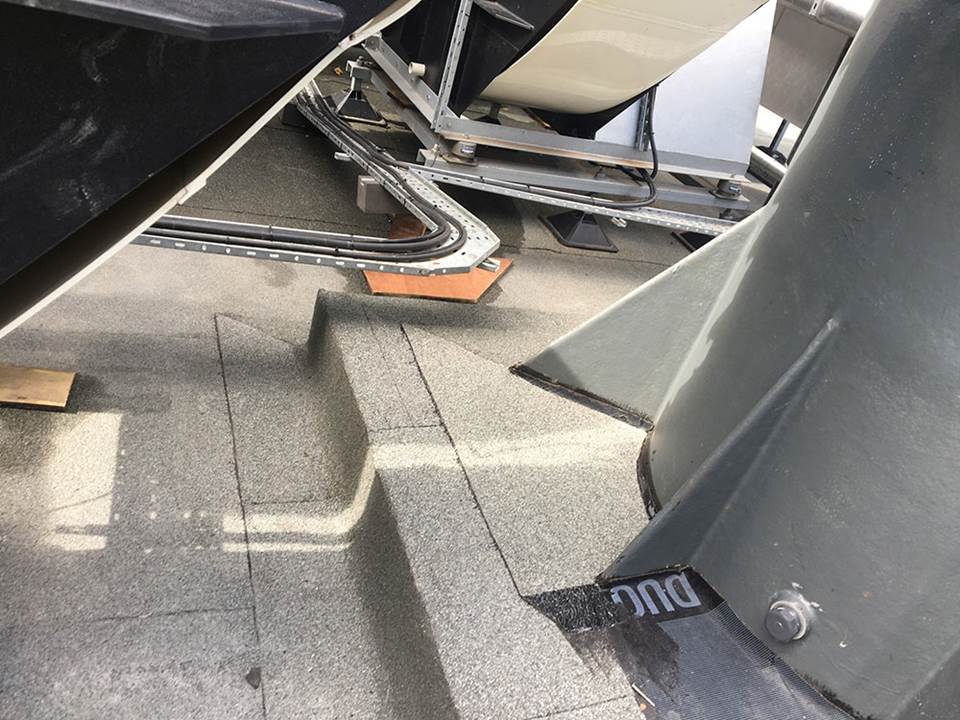
For Kevin Bourne, JPR’s site manager on this project, careful planning and flexibility around bad weather is key to successfully installing a system that can’t be dried with a gas torch. So too is adaptability, which the team demonstrated with the use of safer wet vac and leaf blowers to get 95 per cent of the roof dry.
This isn’t the first Safe2Torch project that the team has worked on, JPR having started adopting Safe2Torch specification since the guidance was released in July 2017. The team is therefore used to this way of working and they prefer it, especially on complex details. The installers had certainly achieved a high level of finish, especially given the number of obstacles in their way.
I was particularly impressed with their setting-out skills, even down to the headlaps all being in a straight line under the plant–just because no one will ever see it doesn’t mean you shouldn’t take pride in your work.
It was not only good to see installation skills at this high level of competence, but to see and hear from Pat and Kevin about how they view Safe2Torch and the changing installation methods for RBM membranes as a positive move forward for the industry.
Final word to Pat: “I like it that the industry is moving forward to safer installation methods that drive up safety, the challenge is to ensure everyone works to the same standards to ensure we make roof fires a thing of the past.”